Simcenter 3D
Structural Simulation
Simcenter™ 3D software for structural simulation offers a set of structural finite element (FE) solvers that form part of the Simcenter portfolio of simulation tools. They are used by engineers across all industries as part of their product development process to assess the structural performance of their systems.
Integrating the Simcenter Nastran solver , Simcenter 3D structural solutions offer scalable, open, and extensible capabilities for general and advanced analysts. They can be used on laptops, workstations and servers to tackle everything from small models to the largest high-end industrial models. Simcenter Nastran is available with enterprise licensing, which means it can be used independently of Simcenter pre/post solutions and can run on both Windows and Linux operating systems.
Benefits of the solution
Reduce risk using simulation to save time and cost
Accelerate innovation with rapid iterations
Investigate product performance under virtually operational conditions
Co-simulação com Simcenter Nastran
Uma plataforma para simulação multidisciplinar
-
Reduce risks and costs while developing innovative frameworks
-
Investigate product performance under virtually all possible operating conditions, including thermally influenced operating conditions
-
Get more accurate solution results than linear analysis when default linear assumptions are invalid
-
Increase confidence in final designs by virtually investigating your product's performance under all possible operating conditions
Simcenter 3D software addresses the engineering of complex products, offering significant improvements in simulation efficiency. With advanced capability 3D simulation technologies and powerful model preparation technology, Simcenter 3D offers new methods that increase realism and provide better insight.
Synchronous technology in Simcenter 3D helps reduce the time spent abstracting the model and editing geometry.
Meshes, loads, and boundary conditions are all associated with the basic design, so when your design topology changes, you can quickly update your simulation results. Solvers and analysis tools provide all the accuracy and speed you need for timely, simulation-driven insights.
Simcenter 3D includes solvers that let you dive deep into physics. Every application specialist will find cutting-edge technology that fits the problem – static or dynamic, linear or non-linear, composite or otherwise, including temperature-dependent materials and thermal loads acting on a structure.
In addition to structural solutions, Simcenter Nastran also allows the co-simulation of structural, thermal and flow physics. A dedicated multiphysics environment allows you to define the complete solution in a single model, making co-simulation easily accessible to a wide range of users.
The Simcenter 3D structural simulation solution is part of a larger multidisciplinary simulation environment and is integrated with Simcenter 3D Engineering Desktop at the core for centralized pre/post processing for all Simcenter 3D solutions. This integrated environment helps you achieve faster CAE processes and streamline multidisciplinary simulations that integrate structural simulation with other disciplines such as thermal simulation, fluid dynamics, multibody dynamics, or electromagnetic simulation.
Industry applications
Simcenter Nastran helps engineering manufacturers and vendors across many industries with their critical engineering computing needs so they can produce safe, reliable and optimized designs in ever-shorter design cycles.
Fuselage - Aerospace and defense - Air engines
Automotive - Land Vehicles
Marine
Electronics
Consumer goods
-
Airplane frame – Rigidity, frame durability, modal frequency
-
Wings – Rigidity, skin buckling, modal frequency
-
Airplane hatch - Seals, structural strength
-
Airplane pylons, ailerons , stabilizers – Rigidity, strength
-
Satellite – Heat stress and distortion, composites, modal frequency
-
Launch Vehicles – Thermal Stress, Maneuvering Loads, Payload Racket Loads
-
Launch structures – Wind loads, launch loads
-
Aerodynamic Engine Fans – Rotating Loads, Distortion, Compounds
-
Air Engine Compressor - Rotating Loads, Stress and Thermal Distortion, Life, Bolt Stresses, Cyclic Symmetry, Shaft Symmetry
-
Aircraft Engine Turbines - Rotating loads, thermal stress and distortion, life, creep, cyclic symmetry, shaft symmetry, failure modeling
-
Aircraft Engine Frame – Rolling loads, switching loads
Sectors
-
Body – Roof crush, panel strength, rigidity, frame durability
-
Power Train/Driveline – Torque Loads, Thermal Stress and Distortion
-
Chassis - Hardness loads, suspension deflections
-
Off-road vehicles – Strength, durability, Rollover Protective Structures (ROPs), stability
-
Fabrication tools – Thermal stress and distortion, modal frequency, bolted stresses
-
Support structures - Stability, stress
-
Full Ships – Rigidity, deformation, strength
-
Hooves - Breaking of the skin
-
Bulkheads - Structural strength
-
Portable equipment – Drop simulation, plastic component stress
-
Printed Circuit Boards (PCB) – Thermal stress and distortion, solder joint strength
-
Electronic boxes - Bracket resistance, modal frequency
-
Packaging – Resistance, stability, hyperelasticity, fluency
Modules
Simcenter 3D Structures software is a unified, scalable, open, and extensible 3D computer-aided engineering (CAE) environment for simulation analysts. Simcenter 3D Structures is a package that combines Simcenter 3D Engineering Desktop, Simcenter Nastran environment and Simcenter Nastran Basic solver . Together, Simcenter 3D Structures provides best-in-class simulation modeling with the power to perform basic structural analysis with an industry-standard solver . The Simcenter 3D Engineering Desktop contained within Simcenter 3D Structures accelerates the simulation process, helping you efficiently build the simulation model you need from 3D geometry faster than traditional CAE preprocessors. THEThe Simcenter Nastran solver built into Simcenter 3D Structures allows you to seamlessly submit analysis models for static linear analysis, normal modes, buckling, and basic heat transfer. Simcenter 3D Structures also forms the foundation on which you can add additional solutions for dynamic structural, multi-step nonlinear, thermal, flow, acoustic, motion, optimization, and multiphysics analyses, all in a single environment.

Simcenter Nastran enables you to initiate digital simulation into your product development process, providing access to a large library of finite element types and material models, robustly handling load cases, and providing multiple sequences of efficient solutions for analysis. in models of unlimited size. You can also perform sensitivity studies based on these types of analysis.
Simcenter Nastran base license comes with a complete base set of structural features as an entry point to Simcenter Nastran. It also comes with a basic heat transfer solver and the resulting temperatures can be used as loads in a structural solution.

Simcenter Nastran Multistep Nonlinear is an advanced solution that provides comprehensive capabilities for geometric nonlinear, contact, plasticity, creep, hyperelasticity, and other material behaviors. The multi-step solution allows users to configure sequential subcases for preload, nonlinear static, nonlinear transient, modal, buckling, postbuckling, and harmonic modes.
This is an add-on product to a base license that offers two non-linear solution options: Simcenter Nastran SOL 401 and SOL 402 solution. Both are suitable for a wide variety of non-linear problems, but each also has unique capabilities.

Simcenter Nastran DMP is a complementary module to Simcenter Nastran Basic. It allows parallel processing using distributed memory. It is an efficient approach to solving large models and can be used on multiprocessor workstations using Windows. DMP solutions are available for static solutions (SOL 101), eigenvalue modal solutions (SOL 103), dynamic response modal solutions (SOL 111 and 112), direct frequency solutions (SOL 108) and non-linear solutions (SOL 401 and SOL 402). DMP can also be used in combination with SMP, which comes as part of Simcenter Nastran Basic.
Module benefits:
-
Accelerate simulation processes by up to 70 percent
-
Perform accurate and reliable structural analysis with built-in Simcenter Nastran Basic solver
-
Increase product quality by quickly simulating design compensation studies
-
Reduce overall product development costs by reducing costly and late design change orders
-
Efficiently manage large and complex analysis models
-
Capture and automate commonly used best practices and processes
-
Easily add multidisciplinary simulation capabilities as your analysis needs grow
Main features:
-
Complete software package with Simcenter 3D Engineering Desktop for pre/post along with Simcenter Nastran Basic for structural analysis
-
NX is a leading geometry kernel that is used as part of Simcenter 3D to provide fast geometry editing and abstraction
-
Comprehensive mesh tools combined with efficient FE assembly management
-
Immerses engineers in the Simcenter Nastran environment using familiar terminology and broad support of product-specific elements and entities
-
Simulate structural analysis for linear statics, normal modes, buckling and heat transfer using the reliable Simcenter Nastran solver
Module benefits:
-
Reduce risk by using simulation to save time and cost compared to physical test cycles
-
Accelerate innovation with rapid iteration and multiple what-if studies
-
Investigate product performance under virtually all possible operating conditions, including thermally influenced operating conditions
Main features:
-
Linear statics, normal modes, buckling
-
Project sensitivity
-
Basic non-linear
-
composites
-
Shared memory parallel processing (SMP)
In addition to the basic feature set, users can add more advanced structural features, including:
-
Non-linear multistep (static, transient)
-
Distributed memory parallel processing (DMP)
-
Linear dynamics (transient, frequency, random)
-
Rotor dynamics
-
Design and topology optimization
-
Aeroelastic
-
Vibroacoustic
Module benefits:
-
Use the same models already built and analyzed linearly with Simcenter Nastran Basic
-
Increase confidence in final designs by virtually investigating your product's performance under all possible operating conditions
-
Get more accurate solution results than linear analysis when default linear assumptions are not valid
Main features:
-
Static/dynamic analysis of models, including material and geometric nonlinear behaviors
-
Multi-step solver allowing the following types of analysis in different steps: static, dynamic, preload, modal, buckling, cyclic symmetry, Fourier harmonic modes
-
Non-linear material: hyperelasticity models (Mooney-Rivlin, Ogden, hyperfoam, Mullins effect, damping with Prony series), elastoplastic (Von Mises yield criterion, isotropic stiffening, kinematic stiffening, mixed stiffening), thermal elastoplastic, creep, creep combined and elastoplastic
-
Nonlinear geometric: large strains, large strain, snap-through (post-buckling) analysis, follower forces
-
Contact: shell and solid element face contact, edge contact for axisymmetric modeling, one- and two-sided contact, self-contact, various friction models, bound contact, contact surface offsets, clearance elements, contact on/off by subbox, contact pressures and force results, contact separation and slip results
Module benefits:
-
More cores provide faster solutions
-
Allows solving large models that are not possible to solve in a single central processing unit (CPU)
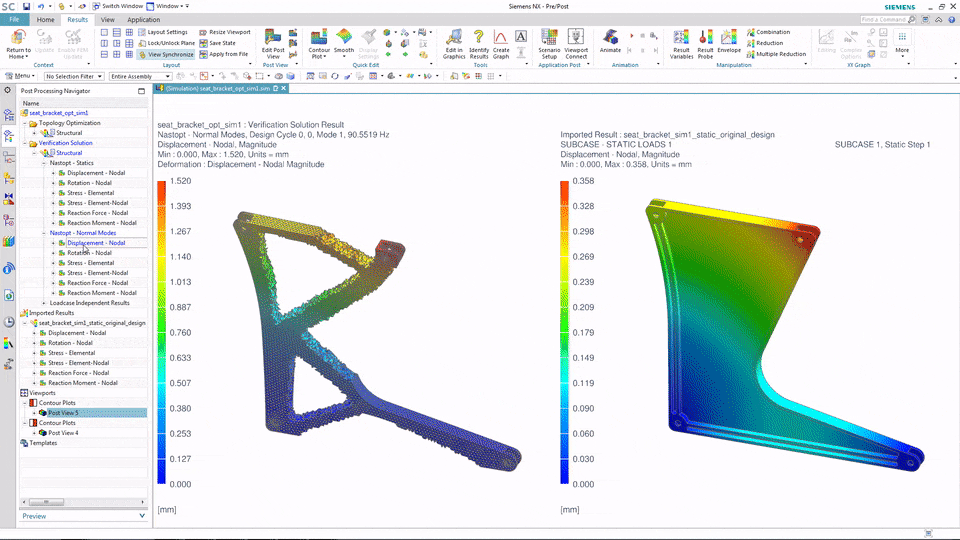
___________________________________________________________________________
Simcenter Nastran
___________________________________________________________________________
Simcenter Nastran Multistep Nonlinear
___________________________________________________________________________
Simcenter Nastran DMP
___________________________________________________________________________
Simcenter 3D Structures