
FloEFD
FloEFD is a commercial software for computational fluid dynamics (CFD), capable of analyzing a wide variety of phenomena involving Fluid Mechanics, Heat Transfer, Optical Analysis, among many other functionalities. Its development, together with several CAD packages such as Solid Edge, NX, SolidWorks, Catia, Creo/Pro-E, facilitates CAD/CAE integration in the most diverse projects focused on fluid dynamics, such as aerodynamics, flow machines and heat exchangers. heat, covering several industrial applications.






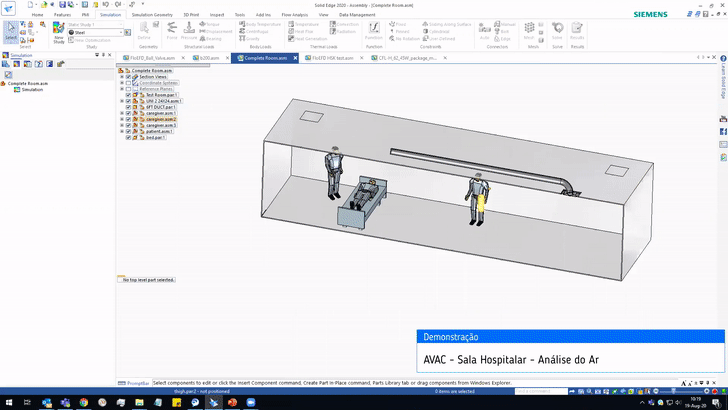
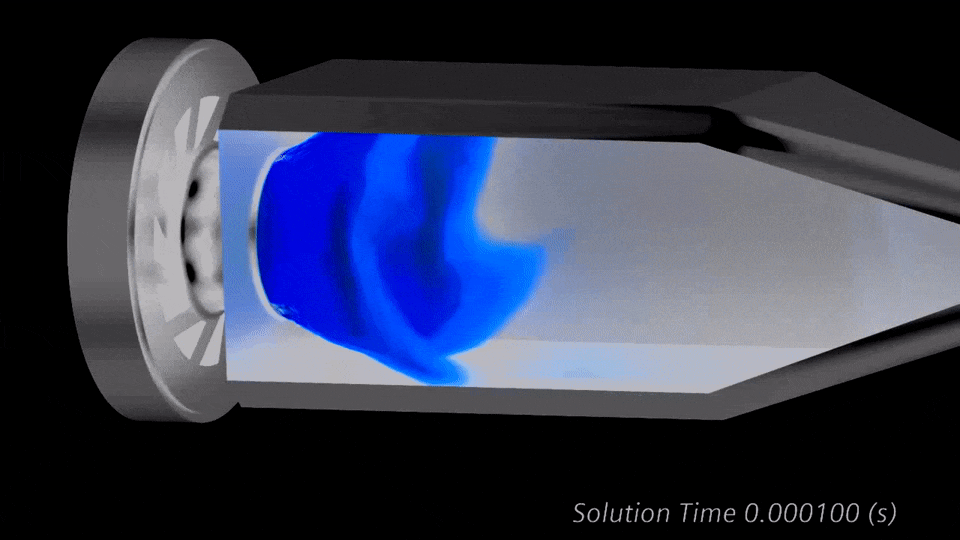

Integrated with CAD
Innovative workflow
Mesh generation
Engineering database
Integration with FloMASTER
Cooling of electronic components
HVAC
Compressible flows and combustion processes
FloEDA module
Because it is integrated into CAD packages, FloEFD offers a friendly and intuitive interface that allows the designer to select and change simulation parameters such as dimensions, boundary conditions, mesh generation, analysis types and material properties in a simple and fast way. .
Mesh generation in FloEFD is one of the software 's differentials , as it works with Cartesian meshes due to its robust and simplified algorithm, which requires less computational time. This mesh, despite having a simplified construction, respects the conditions imposed by the simulation. The mesh has three different types of elements: solid materials, fluid cells and partial cells – which aim to optimize wall effects at the solid-fluid interface, which gives a good advantage to the simulation.
In addition, simulation options interact directly with Excel, allowing instant acquisition of simulation data into an automatically generated spreadsheet; it also offers the possibility of working via external algorithms through the VBS language.
The FloEFD has the Front Loading software feature , which refers to the ability to practice CFD during the design process, i.e., model and simulate simultaneously. Through FloEFD and its interchangeability between CAD software , the design process becomes leaner compared to traditional design. In this way, it allows the optimization of the product, since it integrates geometric modeling, simulation and data analysis in just one software , avoiding rework, whether in geometric modeling or simulations, obtaining greater dynamism for those who work in projects and simulations engineering and ensuring safety and accuracy of results.
Unlike other CFD software , which use tetrahedral meshes, FloEFD features a body-immersed Cartesian mesh structure . This type of mesh allows the designer to reduce the process of trial and error, common to CFD simulation processes, in which an attempt is made to obtain a precise mesh for boundary conditions close to the walls, where the fluid velocity gradients are very high. Such a mesh ensures fast convergence and the number of cells is considerably less, as there is no need to match the mesh with the CAD.
Offering an extensive library for applications in material selection, boundary conditions, porosity, radiative properties, among others, FloEFD also has the option of creating custom materials or conditions, adapting them to the physical properties favorable to the simulation, such as density, conductivity, specific heat, and saving them in the library for future applications.
In practice, the flows that occur in pipes, flow machines, heat exchangers are too complex for an analytical analysis, like traditional 1D flow models. With FloEFD, it is possible to obtain views of the 3D flow in components, which, from a parametric analysis of the results, can be exported in data for analysis in the FloMaster software. Furthermore, FloMaster works with statistical algorithms that combine several configurations ( Latin-Square ), given input values, making the combination of 1D and 3D simulations a powerful tool in the quest to obtain the best performance of thermal systems.ting at steady state. For this, it has an extensive library of materials aimed at the application of electronics by the Engineering Data Base , which can be applied to the components of the analyzed system.
FloEFD is enabled to calculate the effects of heat dissipation on electronic components operating at steady state. For this, it has an extensive library of materials aimed at the application of electronics by the Engineering Data Base , which can be applied to the components of the analyzed system.
For the HVAC designer, FloEFD allows setting boundary conditions according to the situation obtained, be it in industrial operations, where you want to cool equipment by ventilation, or in hospitals, where you have a cooled air network for health reasons.
Flow with complex conditions, fan models, simulation of relative humidity and condensation, performance of heat exchangers, pressure drops in pipe networks, and radiative models for analysis of the incidence of radiation are some of the devices that FloEFD offers to engineers.
This module makes it possible to understand phenomena related to combustion reactions, such as burning propagation, post-burning gas formation, fuel-air mixture effects and mass fractions of gases from combustion; in addition to aspects related to compressible flows, whether subsonic, transonic, supersonic or hypersonic, in order to analyze the effects of Mach numbers, atomic dissociation and ionization by hypersonic flows at high temperatures.
This extension allows you to carry out a thermal analysis of integrated circuit boards, by importing material data, power maps , thermal regions and connection networks from software such as Mentor Expedition, Cadence, Zuken and Altium, avoiding the use of IDF files. FloEDA allows detailing PCB's with materials and thermal properties for the model to be passed to FloEFD for subsequent thermal analysis.